INTRODUCTION:

It is developed by Frederick Taylor (1856-1915), leading proponent of scientific management.
According to Taylor , " Scientific management means knowing exactly what you want men to do and seeing that they do it in the best and cheapest way."
EVOLUTION :
In the earlier days of the industrial Revolution , in the absence of an established theory of factory organisation , factory owners or managers relied on the personal judgement in attending to the problems they confronted in the course of managing their work .
This is referred to as "RULE OF THUMB "
Managing factories by rule of thumb enabled them to handle situations as they arose but suffered from the limitation of trial and error approach .
For their experiences to be emulated , it was important to know what works and why does it work . For this , there was a need to follow an approach that was based on the method of science - defining a problem , developing alternative solutions , anticipating consequences , measuring progress and drawing conclusions .
In this scenario , Taylor proposed scientific management as opposed to rule of thumb and emerged as the " Father of scientific management ."
PRINCIPLES OF SCIENTIFIC MANAGEMENT :
THERE ARE 4 PRINCIPLES BY TAYLOR :
(1) SCIENCE NOT RULE OF THUMB:
--This principle says that we should not get stuck in a set routine with the old techniques of doing work, rather we should be constantly experimenting to develop new techniques which make the work much simpler, easier and quicker.
--Taylor believed that there was one best method to maximise efficiency and that even a small production activity like loading pigs of iron into boxcars can be scientifically planned and managed .
--This method involved investigation of traditional methods through work-study , unifying the best practices and developing a standard method , which would be followed throughout the organization.
(2) HARMONY , NOT DISCORD:
--As per this principle, such an atmosphere should be created in the organisation that labour (the major factor of production) and management consider each other indispensable.
--There should be complete harmony between the managers and the workers .
--Taylor has referred to such a situation as a ‘Mental Revolution’ and firmly believed that the occurrence of a mental revolution would end all conflicts between the two parties and would be beneficial to both of them.
-- Management should share the gains of the company and at the same time workers must work hard to change the company for good .
EXAMPLE :
In Japanese companies paternalistic style of management is in practice . There is a complete openness between management and workers . If at all the workers go for a strike they wear a black badge but work more than normal working hours to gain the sympathy of management .
(3) COOPERATION, NOT INDIVIDUALISM :
--According to this principle, all the activities done by different
people must be carried on with a spirit of mutual cooperation.
--Competition should be replaced by Cooperation.
--Taylor
has suggested that the manager and the workers should jointly determine
standards. This increases involvement and thus, in turn, increases
responsibility. In this way we can expect miraculous results.
--This can be achieved by :
- Rewarding the employees for their suggestions .
- Workers not going on unnecessary strikes and making unreasonable demands.
- Open communication between management and all staff .
- Equal division of work and responsibility between workers and management .
(4) DEVELOPMENT OF EACH AND EVERY PERSON TO HIS OR HER GREATEST EFFICIENCY AND PROSPERITY :
--According to this principle, the efficiency of each and every person
should be taken care of right from his selection.
--A proper arrangement
of everybody’s training should be made.
--It should also be taken care that each individual should be allotted
work according to his ability and interest. Such a caring attitude would
create a sense of enthusiasm among the employees and a feeling of
belongingness too.
TECHNIQUES OF SCIENTIFIC MANAGEMENT :
THERE ARE 7 TECHNIQUES OF SCIENTIFIC MANAGEMENT :
1. FUNCTIONAL FOREMANSHIP-
Foreman represents the managerial figure with whom the workers are in face to face contact on a daily basis .
Functional Foremanship is an extension of the principal of Division
of Work or specialisation to the shop floor.
Taylor advocated separation of planning and execution functions.
Under planning the following activities took place by the 4 personnel--
- The personnel would draft instructions for workers- Instruction card clerk
- Specify the route of production- Route clerk .
- Prepare time and cost sheet - Time and cost clerk .
- Ensure discipline- Disciplinarian .
Production function would ensure :
- Timely and accurate completion of job- Speed boss .
- Keeping machines and tools ready for operation by worker- Gang boss .
- Ensure proper working conditions of machines and tools- Repair boss .
- Check quality of work -Inspectors .
Foremen should have intelligence ,education, tact , grit , judgement ,special knowledge, manual dexterity and
energy,honesty , good health .
2. STANDARDISATION AND SIMPLIFICATION OF WORK-
Standardization refers to the process of setting standards for every business activity . It is a means of achieving economics of production .
Standardization refers to the process of setting standards for every business activity . It is a means of achieving economics of production .
It implies the physical attitude of products should be such that it meets the requirements & needs of customers.
Taylor advocated that tools & equipments as well as working conditions should be standardized to achieve standard output from workers.
The OBJECTIVES OF Standarisation are :
1 .To reduce the given line or product to fixed and predetermined type, form, design, size, weight, quality etc .
2. To ensure the manufacture of identical parts and components.
3. To ensure that the quality & standards of excellence have been maintained.
4. Standard of performance are established for all workers and machines at all levels.
Simplification is method of eliminating unnecessary diversity of products . It results in saving of cost of labour , machines , tools etc .
Simplification aims at eliminating extra varieties , sizes and dimensions , sizes while standardisation implies devising new varities instead of existing one.
3. METHOD STUDY-
5. TIME STUDY-
7. DIFFERENTIAL PIECE WAGE SYSTEM -
Taylor advocated that tools & equipments as well as working conditions should be standardized to achieve standard output from workers.
The OBJECTIVES OF Standarisation are :
1 .To reduce the given line or product to fixed and predetermined type, form, design, size, weight, quality etc .
2. To ensure the manufacture of identical parts and components.
3. To ensure that the quality & standards of excellence have been maintained.
4. Standard of performance are established for all workers and machines at all levels.
Simplification is method of eliminating unnecessary diversity of products . It results in saving of cost of labour , machines , tools etc .
Simplification aims at eliminating extra varieties , sizes and dimensions , sizes while standardisation implies devising new varities instead of existing one.
3. METHOD STUDY-
This technique determines the best way of doing the job .
There are various methods of doin the job .
To determine the best way there are several parameters . Right from the procurement of the product to the final delivery of product to the customer every activity is a part of method study .
The objective of method study is to minimise the cost of production and maximise thr quality and satisfaction of the customer .
Examples of method study are :
Operations Research and
Assembly lines : Process Charts :
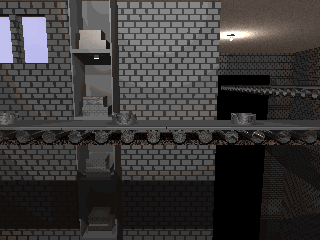
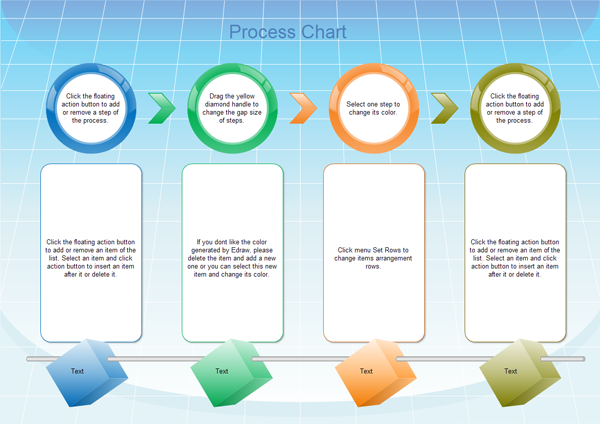
4. MOTION STUDY-
In this study, movement of body and limbs required to perform a job are closely observed.
In other words, it refers to the study of movement of an operator on machine involved in a particular task.
The purpose of motion study is to eliminate useless motions and determine the bet way of doing the job.
By undertaking motion study an attempt is made to know whether
some elements of a job can be eliminated combined or their sequence can
be changed to achieve necessary rhythm.
Motion study increases the efficiency and productivity of workers by cutting down all wasteful motions.
EXAMPLE :
It is possible to find out :
Motions that are productive .
Motions which are incidental ( going to stores ) .
Motions which are unproductive .
Taylor used stopwatches and various symbols and colours to identify different motions .
It is a technique which enables the manager to ascertain standard time taken for performing a specified job. Every job or every part of it is studied in detail.
This technique is based on the study of an average worker having reasonable skill and ability.
Average worker is selected and assigned the job and then with the help of a stop watch, time is ascertained for performing that particular job.
Taylor maintained that Fair day’s work should be determined through observations, experiment and analysis by keeping in view an average worker.
This technique is based on the study of an average worker having reasonable skill and ability.
Average worker is selected and assigned the job and then with the help of a stop watch, time is ascertained for performing that particular job.
Taylor maintained that Fair day’s work should be determined through observations, experiment and analysis by keeping in view an average worker.
Standard Time × Working Hours = Fair Day’s Work
EXAMPLE :
EXAMPLE :
On the basis of several observations it is determined that standard time taken by the worker to make one cardboard box is 20 minutes. So in 1 hour he / she will make 3 boxes.
Assuming that a worker has to put in 8 hours of work in a shift and deducting one hour for rest and lunch , it is determined that in 7 hours a worker makes 21 boxes @ 3 per hour . This is the standard work a worker has to do .
6. FATIGUE STUDY-
6. FATIGUE STUDY-
A person is bound to feel tired physically and mentally if he / she does not rest while working .
The rest intervals will help one to regain stamina and work again with the same capacity . This will result in increased productivity .
Fatigue study seeks to determine the amount and frequency of rest intervals in completing a task .
EXAMPLE :
A plant , work takes place in 3 shifts of 8 hours each .Even in a single shift a worker has to be given some rest interval for their lunch and some other small pauses from the work .
7. DIFFERENTIAL PIECE WAGE SYSTEM -
This technique of wage payment is based on efficiency of worker. The efficient workers are paid more wages than inefficient one.
On the other hand, those workers who produce less than standard
number of pieces are paid wages at lower rate than prevailing rate i.e.
worker is penalized for his inefficiency.
This system is a source of incentive to workers who improving their efficiency in order to get more wages.
It also encourages inefficient workers to improve their performance and achieve their standards.
It leads to mass production which minimizes cost and maximizes profits.